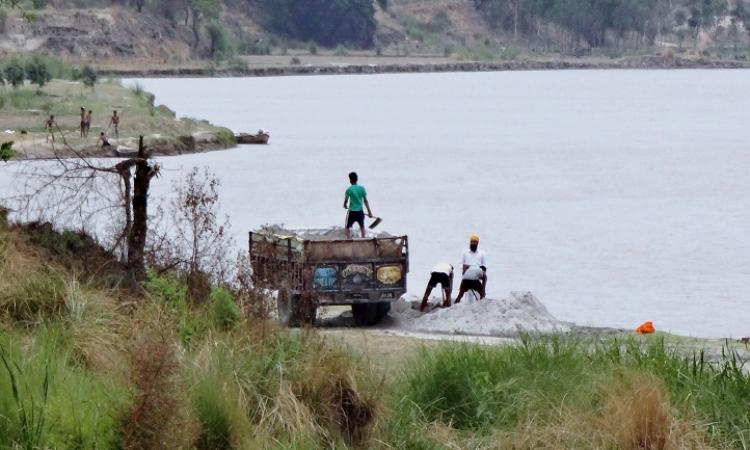
Sand is today the most consumed raw material in the world after water. From building infrastructure to making glass, silicon chips, solar panels and even detergents and toothpastes, sand is an omnipresent element of our living.
Most of the sand grains are quartz eaten away naturally, carried by rivers to be dumped on their beds, flood plains and beaches. It’s little wonder then that most of our sand is coming from riverbeds and sea sides while ponds, tanks and agricultural land remain the secondary sources.
According to the data by the Bureau of Indian Mines, sand production in India touched 13,81,406 tonnes in 2014-15. But this is only about authorised mining. The boom in the real estate sector has increased the demand for sand, resulting in local sand mafias ripping the river beds and floodplains with no regard for natural resources.
This illegal mining is the reason why rivers are changing their courses, their flood regulation capacities are reducing and groundwater levels are receding. At many places, the smaller tributaries have dried up.
This illegal sand mining is happening under the cover of darkness or in connivance with police and government officials. Several upright officials like constable Dharmendra Chouhan of Morena, Madhya Pradesh and concerned citizens like Pale Ram Chauhan of Uttar Pradesh who tried to stop the practice have paid the price with their lives.
Various courts, including the National Green Tribunal, have imposed stricter regulations on sand mining which have led to the drop in the availability of river sand. But considering the real estate sector in India is slated to grow at 30 percent over the next decade, besides public infrastructure like roads, dams and bridges are undergoing expansion, illegal sand mining is bound to prosper, creating greater ecological and social crisis.
M-sand and quarry dust
The quest for alternatives to sand has led to the growth of the manufactured sand industry. The product, also called m-sand, is made by crushing granite or basalt rock to a required grain size. It is considered better than sand as it lacks the inconsistency and impurities present in natural sand.
A 2012 study done at the Indian Institute of Sciences found that the strength of the mortar made with m-sand was 150 percent higher than the mortar made with river sand. There was also greater water retention which improves the strength and the bond development. The cost of m-sand is around 40 percent less than the river sand.
The m-sand producers have grown in numbers and the government subsidies in Karnataka and Andhra Pradesh may further the idea. “The idea has caught the attention in the last one year as the supply of river sand declined due to stricter regulations. However, many stone crushers have started branding their products as m-sand even though it’s of low quality. It’s important that buyers go only for those producers who use vertical shaft impactor which produces the grade of m-sand meeting the specifications of the Bureau of Indian Standards," says Prof. M. U. Aswath of the Bangalore Institute of Technology, who undertook a research for the Indian Concrete Institute to study alternatives to river sand.
Quarry dust, formed during the crushing of the stone, is another alternative. In fact, quarry dust is extensively used as a replacement for sand in the Kutch region of Gujarat. “Though the strength of structures using quarry dust is found to be less than the river sand, it is used a lot because of the easy availability as we have several crushing units in this region,” says Jighnesh Gor of Hunarshala, a Bhuj-based organisation working with the community to promote traditional building techniques.
A 2013 study found that quarry dust can replace sand only between 55 to 75 percent because after that, the workability of the mortar decreases. However, total replacement of sand is possible with the addition of fly ash (a byproduct of thermal power plants) to the mix.
Quarry dust performs better with road construction. “It’s possible to totally replace sand with quarry dust depending on the grade of concrete you want. We are using quarry dust extensively in our project,” says Deepak Gariya who has been working as a planning engineer with India’s longest road tunnel project between Chenani and Nashri in Jammu and Kashmir.
Things to be aware of
There are several other alternatives to sand like foundry sand, slag (byproduct of steel and copper industries) and construction-demolition waste, but these are yet to make a mark as they can neither substantially replace river sand nor are as easy to access as manufactured sand and quarry dust.
The proliferation of concrete which may not meet the specified standards is also a big issue. “People are using all kinds of alternative materials to make concrete nowadays. One way to identify quality concrete is to go for brands which have Ready Mix Concrete Plant Certificates from the Quality Council of India. Also, beware of the dealers selling sand dug out from agricultural fields as river sand. A building constructed from farm sand lacks in durability,” says Aswath.
Alternative to construction?
This search for alternatives to sand apart, we can also look for alternatives to construction. We started using sand only when cement came into the picture. Before that, houses were built using the locally-available materials, be it clay, wood or stone, which were not only well-suited to the local climate but also cushioned against disasters.
One of the best examples is the use of alternate layers of stone and timber in old houses of Himachal Pradesh which can resist the forces of the earthquake. The floors in these houses are made from timber that does not get cold easily. Use of lime as the binding material in ancient stone buildings of Rajasthan, on the other hand, helped deal with hot weather while imparting strength.
Tejas Kotak of Hunarshala, which has been promoting the use of traditional materials for community housing, says even though the current building industry is using concrete extensively, we have to make the shift soon. “I am not against cement. It can be used at places where sand is easily available but what’s the point in hauling materials from distant areas especially when local options are there? Going local is the only way to preserve our rivers and we have to do that someday because the pressure is increasingly being felt,” he says.
Paucity of time and non-availability of raw material is also pushing people towards quick fix solutions. “Steel buildings are picking up fast as they can be erected in less time than concrete structures and don’t need to depend on multiple raw materials,” says Chandigarh-based architect Surinder Bahga.
Perhaps then the alternative is a mix of solutions and not just one. But these have to be adopted quickly before more sand escapes the hourglass of our world.